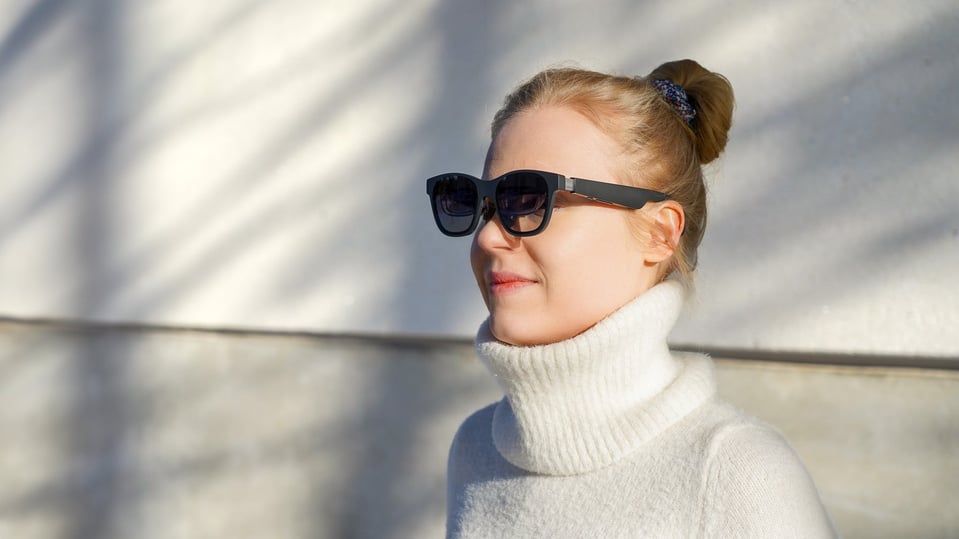
Blogs
Comparing and contrasting different waveguide technologies: diffractive, reflective, and holographic waveguides
Waveguide technology is an important concern for manufacturers of AR devices. While other technologies, such as OLEDs, are more mature, they can be more appropriate for fully immersive VR and XR headsets where transparency isn’t a feature. Waveguide technology- including diffractive, reflective, and holographic waveguides- is useful when the aim is to seamlessly overlay digital images onto the real world, as with AR glasses. AR devices typically require a challenging combination of being transparent, with a wide field of view display, and packaged in a compact form factor. Each waveguide type offers a unique set of challenges and advantages – in terms of optical performance, field of view, form factor, and the relative complexity of the manufacturing process.
Introduction – how do the different types of waveguides work?
A waveguide is a flat, transparent display made from a plate of glass or plastic (polymer). It uses a series of specialized structures called optical elements to guide light from the projector towards the user’s eye. The optical elements are designed to couple light in, out, or change its direction. This enables the projector to be hidden in the temple of the glasses while the user’s view stays unobscured.
Diffractive waveguides use gratings, which are periodic nano-scale structures imprinted or etched onto a resin layer on top of the surface of the glass or plastic (the substrate). The gratings work by diffracting light at specific angles, allowing images to be directed inside the waveguide and finally coupled into the user's view.
Holographic waveguides also work by diffracting light. However, they utilize holographic optical elements (HOEs) to diffract light. The HOEs are recorded as patterns within the resin material itself rather than as physical structures on the surface.
Reflective waveguides use a different function altogether. They are made from stacked arrays of partly reflective mirrors and transparent materials, which are sliced to form the waveguide. The light is guided through a series of reflections from the projector to the user’s view.
Between the optical elements, where there is only plain transparent glass or plastic, total internal reflections (TIR) confine the light within as it moves from one element to another. TIR occurs when light hits the surface of the waveguide at a certain angle, reflecting it entirely rather than letting it escape.
Each waveguide type has its subtypes, which differ in structure, materials, and manufacturing methods. New waveguide technologies are constantly being developed, some of which may not fit into these basic categories or might even be considered a combination of them.
Comparing and contrasting the benefits of each type of waveguide
When it comes to image quality, there can be a big difference between the different types of waveguides.
Diffractive waveguides have an inherent challenge with spectral dispersion – when the different colors of red, green, and blue diverge inside the waveguide. This also occurs in other waveguide types, but diffractive optical elements (DOEs) are more sensitive to it. The user may see an offset image for each color – this might only be noticeable at the very edge of the image, where a color fringe effect may be visible.
The structures on diffractive waveguides vary in shape and performance. The most common structures are called surface relief gratings, or SRGs. These gratings can be shaped, for example, as binary, slanted, or blazed.
The different structures have their own pros and cons. The binary structure is highly manufacturable because it’s a periodic step-like pattern, but it can usually be less efficient at the edges of the field of view (FOV), especially with larger FOV sizes.
To overcome this problem with the binary gratings, blazed or slanted gratings can deliver higher efficiency, but they are more challenging to manufacture and design. The gratings are optimized for a particular wavelength range, so multiple color-specific waveguides might need to be stacked to give the full spectrum of colors. In theory, each grating type can deliver good image quality – but manufacturability and available materials must always be considered.
In holographic waveguides, the structures are recorded within the resin layer as changes of the material’s refractive index. These changes are ‘seen’ by the light as a structure. One example of these structures is volume holographic gratings (VHGs).
In SRGs, the diffraction and TIR occur at the same threshold on the surface of the material where the physical gratings reside. In HOEs, the light gradually deviates in the embedded structure first before reaching the surface where TIR occurs. This changes the sensitivity to spectral dispersion, which could be taken advantage of for optimizing image quality.
However, similarly to diffractive waveguides, combining all colors into a single waveguide can result in significantly lower efficiency and a reduced field of view (FOV) compared to using color-specific waveguides.
The pros and cons of reflective waveguides mostly involve the manufacturing process and physical size. They offer the best color uniformity since they use reflections and minimal spectral dispersion. However, when coating mirrors and stacking them, if the mirror surface isn’t completely uniform and stacked in alignment with the other mirrors, it can cause issues in the modulation transfer function (MTF) – essentially, the sharpness of the image. The physical size of the waveguide can also increase due to the mirrors being larger to achieve larger FOV and eyebox. However, it’s more efficient because it reflects all the wavelengths at once, whereas with diffractive and holographic, you’re optimizing for a specific wavelength range and lose efficiency due to diffraction.
For the most part, these waveguide technologies are equal in form factor—weight and size—or if there are differences, they are very small compared to a full VR/XR headset. So that might not be the first consideration when choosing between them.
Market readiness
The principles of all three waveguide technologies were invented tens of years ago in research settings. However, their market readiness for AR differs.
Diffractive waveguides have multiple examples and have been on the market for years. They’re widely available off the shelf -- Microsoft HoloLens and Magic Leap are a couple of examples.
Holographic waveguides have more complex designs, and there isn’t widespread market adoption yet—but DigiLens uses them. Lumus uses reflective waveguides, but technology adoption of off-the-shelf glasses is still ongoing.
Examining the challenges in the manufacturing process for each waveguide technology
For diffractive waveguides, nanolithography can be used to transfer the designed gratings onto the raw material. First, the glass or plastic must be coated with something sensitive to light—usually a liquid, such as a photosensitive resin. For diffractive SRGs, nanoimprint lithography can be used, and a hard master with the gratings is created to stamp the structures over and over onto the new pieces of glass or plastic.
Nanoimprint lithography is a physical process that entails a stamping process called imprinting, and it can create a physical strain on the structure. To prevent the hard master from degrading, an intermediate soft stamp is made from it, which is then used to imprint the actual waveguides instead of the hard master.
For holographic waveguides, because the HOEs are within the volume of the photosensitive material, interference lithography can be used to record the structures inside the material. Through interfering laser beams, nano-scale patterns are exposed within the volume. Depending on the material type, exposure can alter the refractive index of the exposed areas, creating a structure ‘seen’ by light. Since the pattern transfer is less physically straining than the stamping in NIL, it allows for using other manufacturing techniques, such as roll-to-plate and roll-to-roll.
Because the structures for both diffractive and holographic waveguides are nano-sized, getting repeated results that are replicated repeatedly can be a challenge.
Reflective waveguides are not strictly nano-sized processes; rather, they require more of a mechanical process of stacking the partly reflective mirrors and cutting them. While stacking mirrors in the same orientation is simpler, improved designs might require a more complex arrangement of the mirrors. Getting reliable and consistent results on a large scale while reducing physical defects in the samples is a challenge.
In all three of these processes, the materials are costly and constantly under R&D. Glass, resin, and different coating materials have all been researched heavily to make them better, more reliable, and able to work in extreme conditions. For the manufacturer, making them more affordable, so they can be built at scale, is critical.
Which of these different waveguide technologies could become the gold standard in the market?
As with most technology markets, it can be risky to make predictions, but generally, the technology that wins any race is the cheapest to make, with the most robust way of delivering a good user experience.
The price is the biggest issue in all these technologies. The manufacturing tools, processes, and materials are expensive to purchase, and the manufacturing process is costly to set up. This is why the price of individual AR displays remains high to this date.
If one player could uncover a way to bring the price down tenfold, that would make the case for that technology to dominate the market. The possibilities for bringing down the cost entail making materials more available and commonplace, the manufacturing tools more capable of running bigger batches, and manufacturing processes more slimmed down for greater throughput.
The final verdict?
It is still an open question which waveguide technology will become the most dominant. At the recent SPIE 2024 industry conference and exhibition, all of the waveguide technologies were being displayed by the largest players in the space. At OptoFidelity, we continue supporting all waveguide technologies through our state-of-the-art testing equipment. Therefore, OptoFidelity is in an excellent position to offer non-biased opinions and guidance in this market. We will continue to provide you with updates as the market changes.
Written by