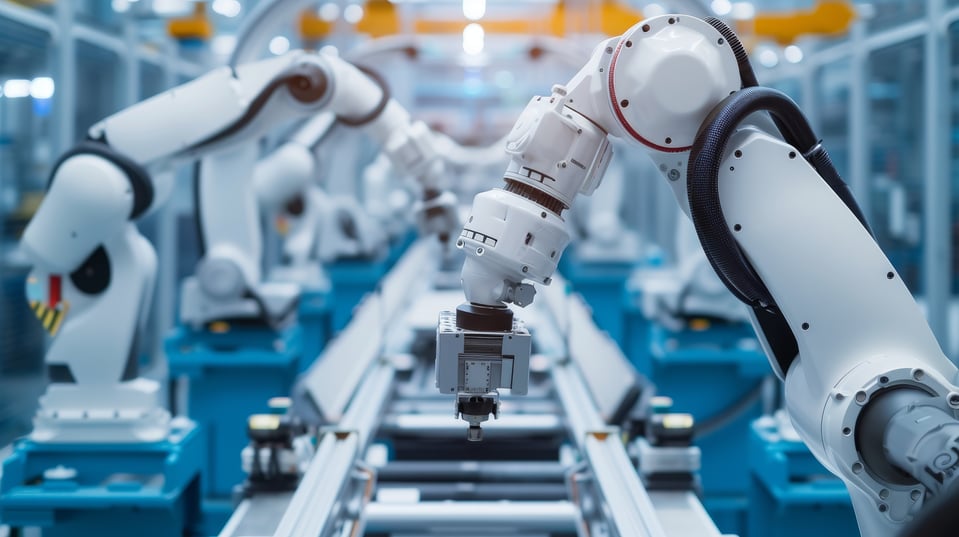
Blogs
Explaining the importance of correlation between R&D and manufacturing of XR waveguides
As the AR / VR / XR industry grows, it requires precise image quality measurements to build high-quality devices in a volume manufacturing environment. Until now, many XR manufacturers haven’t had the possibility of volume manufacturing. The industry has been focused on fine-tuning waveguide technology in an R&D environment. This is all changing, as market demands increase, and as manufacturers have the possibility of producing a large volume of devices.
The principles of testing waveguides for XR devices remain the same in the R&D phase as production phase, but the primary objective is very different. In production environments, the manufacturer is interested in testing waveguides to see if they will pass or fail an acceptable range of image quality. This range should be previously defined in the R&D environment, where a wide variety of measurements are necessary to determine the quality of the waveguides across many parameters.
During R&D, designs are being sampled, and materials are being explored. The metrology testing at this phase could be looking at upwards of 20 parameters (see graphic below) at different eye-box positions – asking for the utility of each parameter in defining the overall quality of the waveguide.
Once it moves into the production phase, these parameters are boiled down into a simple pass/fail system which is asking: Is this waveguide within the acceptable range for the best end-user experience?
At OptoFidelity, our metrology uses the most precise measurement tools on the market today – and our measurements, and test results, are the same across both R&D and production environments. This correlation is critical to making volume production a reality.
Why does correlation matter between R&D and production?
The important parameters tested on waveguides are determined in the R&D environment, and these parameters used to define the pass/fail system required in the high-throughput, high-speed production environment. If these two environments aren’t correlated, the results will not match seamlessly together.
If questions arise in production that haven’t been explored previously in R&D, this exposes the process to wasted time, wasted materials, and increased expense.
Because our Production IQ Test System (for volume manufacturing) correlates precisely with WG-IQ (for R&D phase), these questions are posed continually throughout the process, with correlated results.
What matters the most to manufacturers of XR devices? Data quality
XR manufacturers need access to reliable data. If a waveguide is found to be sub-optimal, it's crucial to address the issue as early as possible in the production line.
This means having data that is accurate and well-calibrated. In optical metrology, this depends on having the best equipment available today – such as what we use at OptoFidelity. Our high-quality measurement instruments include OptoColor – our measurement camera – and OptoProjector. In addition, it’s important to have precise optical alignment of the metrology system. For this, we utilize autocollimators, bringing the top specification available today.
How do manufacturers strike a balance between quality and throughput
Because our R&D and production phase measurements are correlated, we can assist manufacturers with one of the trickiest elements – ensuring a balance between a commercially viable manufacturing process and setting the standard for high-quality outcomes.
That’s why it’s so important that parameters be defined in R&D to set a range for pass/fail in production. Once the waveguides are going through the high-speed production environment, the manufacturer doesn’t need as precise a picture of waveguide image quality at various eye-box locations and different measurement parameters – because that would make the process less cost-effective and too time-consuming. At that point, the manufacturer must have narrowed it down to the critical measurement parameters such that a pass/fail indicator is enough to determine adequate waveguide image quality.
In this way, optical metrology ensures that a balance can be achieved, and volume manufacturing can become a reality.
Written by