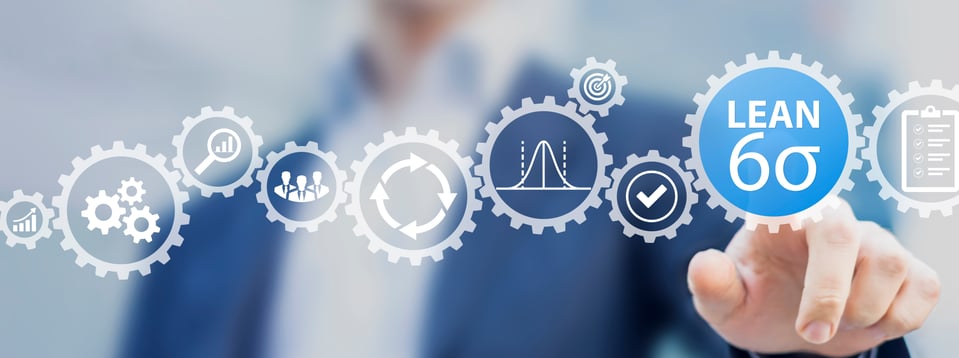
Blogs
Reducing Idle Time in the Manufacturing Process of Waveguide Technology
When producing waveguide technology for AR and VR headsets and glasses, manufacturers are concerned with keeping costs as low as possible, while maximising efficiency and output. This means that eliminating faulty outcomes in the production process is of paramount concern for Quality Control.
Value-Added Time (VAT) is a critical concept in Six Sigma, aligning with the methodology’s focus on process improvement and waste reduction. VAT is considered the time in the manufacturing process during which actual value is added to the product though product waiting time for example in between two process phases is non-value adding time. OptoFidelity is uniquely positioned to minimise non-VAT in volume manufacturing of waveguide technology for AR and VR devices.
The first step in minimizing non-VAT lies in reducing idle time in the manufacturing process. Waveguides are complex to fabricate, and the production process involves sensitive steps where faults can creep in.
Metrology – or the testing of the product throughout the manufacturing process – ensures samples are error-free. Automated testing tools are critical in this process – and metrology must be incorporated throughout the entire process to reduce errors.
For example, stacking can be a part of the production flow of full-colour AR displays. By stacking color-specific diffractive waveguides together, better efficiency and larger FOV can be achieved for the final display. However, stacking of the waveguides is a sensitive process, with potential yield loss or loss of time. Prior to permanently gluing together the red, green, and blue specific plates, it’s critical to test single units for quality early in the process. It could happen already on the wafer level or after dicing on the plate level. To the human eye, the wafer might look perfect, but perhaps the gratings are not replicated deeply enough, or maybe the orientation is off – problems that would lead to poor image quality.
Parameters such as grating depth and orientation can be classified as Critical to Function (CTFs). They are essential for the core functionality of the display but are often not visible to the end-user. Image and cosmetic quality are Critical to Quality (CTQs) and are directly observable by the end-user.
Both CTFs and CTQs need to be first mapped for every process and then a control plan for them is established. In the production flow, this can mean they are tested and measured before proceeding to the next process step, preventing the further loss of costly materials and time.
Each wafer could contain anything between a single waveguide up to more than ten waveguides depending on the wafer diameter. The back-end process steps commonly involve dicing, cleaning, edge blackening, and stacking. Those subsequent steps could potentially be wasted on a low performing sample, if CTFs and CTQs weren’t checked early enough.
Frequent and fluent testing ensures that any units that aren’t meeting the quality standards can be taken out of the material flow early. Extensive measurements is not target itself but can be simplified between process steps if the process is under control and the relationships between causes and effects are well-known.
When quality isn’t controlled in all stages, it could result in the discovery of faults in the end product by the customer. These costly mistakes can be avoided by planning the quality control over the whole end-to-end process.
Another benefit of the automated testing solution is that the robotics can be trusted to place a sample in the same position every time, using markers for alignment. As compared to a human placing them by hand, the robot excels at repeatable and consistent placement.
System stability is maintained not only through automation but also by precise initial alignment and consistent monitoring of alignment status. Therefore, each stage of the testing process is entirely repeatable – it could be rested today, and retested a month later, and it’s done consistently, using the same parameters.
The measurement results contain all necessary data to trace sample performance, and they can be optional viewed in a dashboard environment. With this data, we could query: What did we produce today? What was the quality? Where did we lack and what can be improved? The system's architecture inherently supports integration with manufacturing execution systems, facilitating seamless incorporation into existing production lines.
In summary,
- Speed - The production process of waveguide technology is sped up using robotic automation
- Repeatability and stability – Robotics will place the same unit in the same way every time. Measurements are done at various steps using identical parameters, ensuing results are comparable
- Correlating with the R&D results - OptoFidelity delivers the identical metrology for volume manufacturing as in the R&D tool – so the results and metrics are comparable to the results from the R&D process
- Lowering cost in production – Faulty end-products are avoided because we identify mistakes, and pinpoint where they are happening, on the manufacturing line
- Integration with MES - The automated system integrates with standard manufacturing systems
- Parallel testing - While a sample is waiting for measurement, idle time is eliminated because the tool can make use of between two to four stations at once. The modular system is customizable, and modules can be adapted and changed – future-proofing the tool.
Written by